Introduction: Why Manufacturer Choice Matters in Pressure Vessel Projects
When it comes to stress vessels, deciding on the proper producer is simply as essential as the layout itself. The incorrect provider should end result in pricey delays, protection risks, or non-compliance with ASME standards. Whether you are in the petrochemical, strength generation, LNG, or nuclear sector, deciding on a stress vessel producer with the proper technical know-how and forging competencies is essential.
In this article, we’ll discover what to seem to be for when evaluating stress vessel producers and how solid aspects play a key position in overall performance and reliability.
What Is a Pressure Vessel and Why Forged Components Matter?
A stress vessel is a container designed to preserve gases or beverages at excessive pressures. Key to secure operation underneath severe stress, the integrity of cast elements like shells, heads, nozzles, and tube sheets without delay influences vessel strength, leak prevention, and longevity.
At TIPTOP FORGING, we specialize in forging high-performance components that meet or exceed ASME Section VIII standards, making sure long-term sturdiness even in the most annoying environments.
Key Factors to Compare When Choosing a Pressure Vessel Manufacturer
1. Certifications & Standards Compliance
Reputable producers ought to comply with:
ASME Boiler and Pressure Vessel Code (BPVC)
ISO 9001 / PED (Pressure Equipment Directive)
API 660/661 (for warmth exchangers)
Look for producers who grant fabric traceability, NDT reports, and third-party inspections on all necessary components.
2. Material Expertise — Including Stainless Steel Pressure Vessels
Materials like carbon steel, low alloy steel, and in particular stainless metal (304, 316, duplex) require unique forging, warmness treatment, and machining knowledge. Ask if the producer has trip in corrosion-resistant, high-pressure, and high-temperature vessel applications.
Critical Forged Components to Evaluate
✅ Shell Courses (Heavy-Walled Shell Rings)
Ideal for thick-walled vessels used in LNG storage tanks, hydrotreating reactors, and coal liquefaction units. These large-diameter forgings grant energy and uniformity that rolled or welded plates frequently lack.
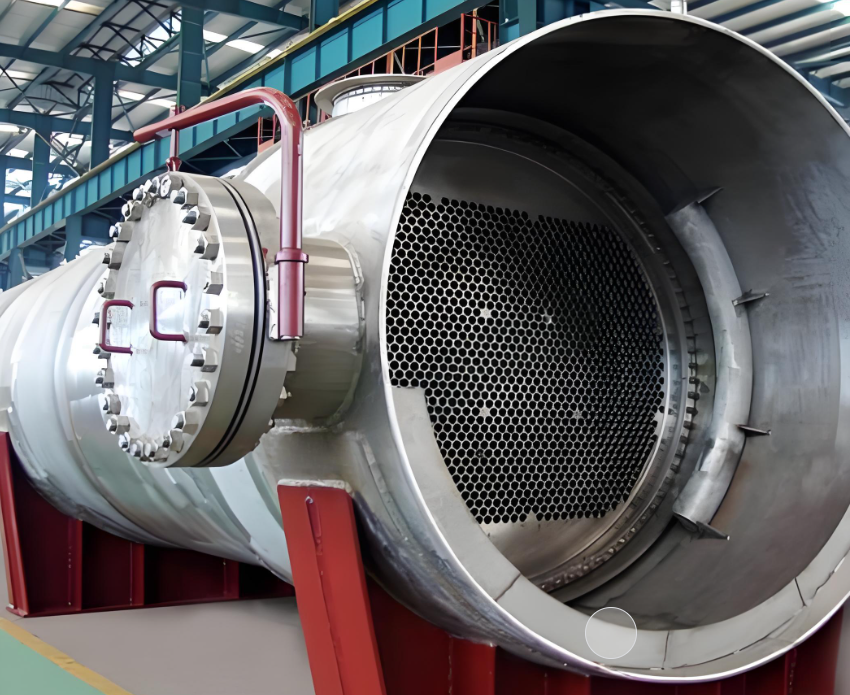
✅ Head Forgings (Elliptical, Torispherical, Spherical)
Forged head blanks make sure dimensional precision and crack resistance underneath excessive pressure, imperative for reactors and nuclear vessels.

✅ Tube Sheets
Used in warmth exchangers and boiler drums, cast tube sheets face up to warping, thermal fatigue, and stress corrosion cracking.
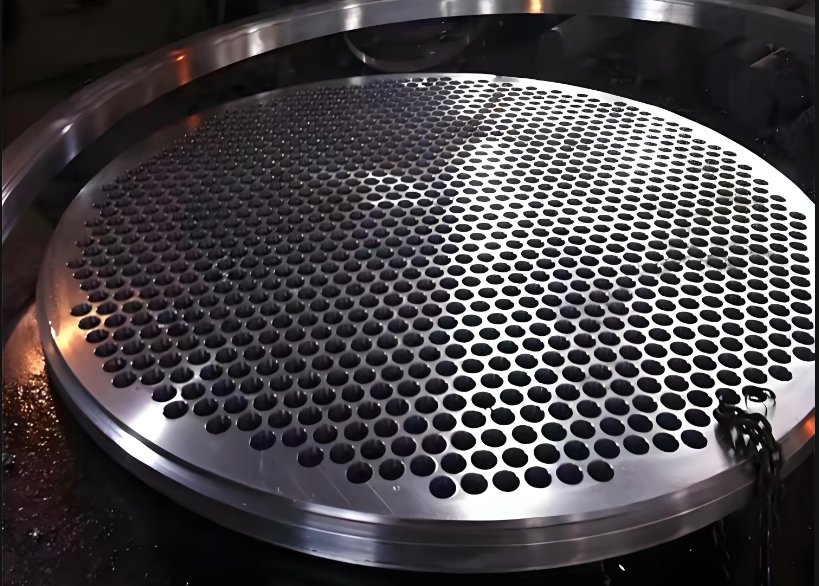
✅ High-Pressure Flanges (Class 1500 / 2500)
Large-diameter flanges for imperative stress joints have to be exactly cast to assurance sealing overall performance underneath fluctuating conditions.
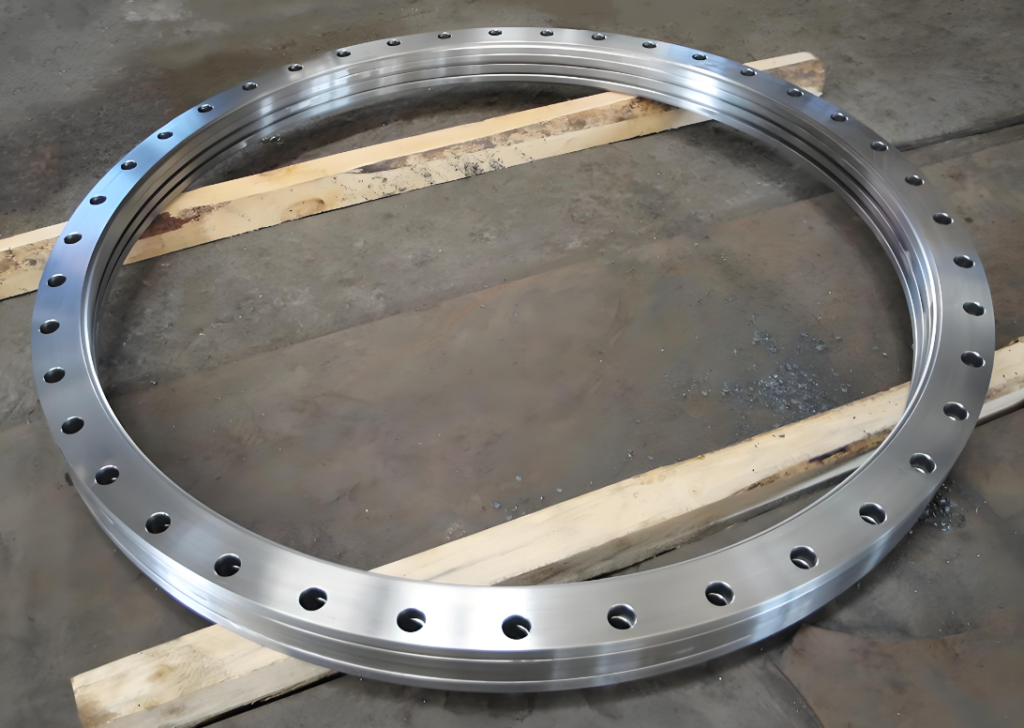
✅ Nozzle & Manway Forgings
Custom, thick-walled nozzle forgings grant invulnerable integration factors for piping structures and instrument access. Especially indispensable in high-pressure, high-cycle environments.
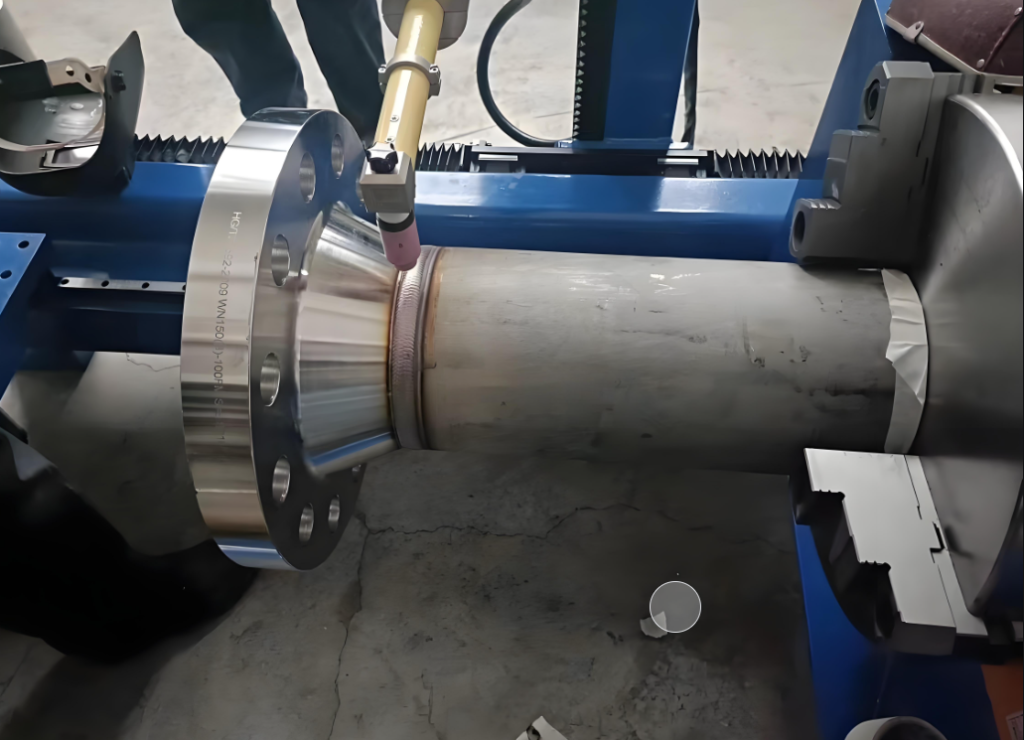
✅ CMT / SIT Shell Forgings (Nuclear)
If you are in the nuclear industry, appear for suppliers skilled in cast shell sections for Core Makeup Tanks (CMT) and Safety Injection Tanks (SIT) — the place zero failure tolerance is the standard.
Why Forging Outperforms Casting or Fabrication
In strain vessel manufacturing, forging presents key blessings over casting or welding:
No interior porosity or shrinkage defects
Superior mechanical residences (yield strength, toughness)
Enhanced grain shape for fatigue resistance
Consistency in thickness, shape, and integrity
That’s why main stress vessel producers depend on cast rings, discs, and flanges — in particular for high-pressure, high-temperature, or mission-critical applications.
Questions to Ask Your Pressure Vessel Manufacturer
Before putting an order, consider your provider with questions like:
What forging approaches do you use for shell rings and heads?
What stainless metal grades are handy for stress vessel components?
Do you assist nuclear-grade forging production?
Can you personalize tube sheet or nozzle gap layouts?
Conclusion: Choosing a Manufacturer That Strengthens Your Vessel from the Inside Out
Not all strain vessel producers are created equal. Forged exceptional starts offevolved deep interior — with precision, fabric science, and strict compliance. From high-pressure flanges to nuclear-grade shell forgings, our organization gives you the heavy-duty factors that make your vessel safe, strong, and long-lasting.
Ready to Partner With a Trusted Pressure Vessel Forging Expert?
We assist petrochemical, LNG, and nuclear industries meet their most complicated forging needs. Let’s speak about your project.
[Contact Us Today] to get a quote for your strain Pressure Vessel components.