When engineers search for forging products, they’re searching for reliability underneath stress—components that won’t crack, deform, or degrade over time. At Tiptop Forging, we manufacture components that constantly outperform forged or machined alternatives, handing over the strength, durability, and protection modern-day enterprise demands.
What Defines a Forged Product?
A forging product is created by using deforming stable metal—often a bar, billet, or ingot—under excessive strain to shape a preferred shape. Unlike casting, forging retains the metal’s grain structure, producing:
Aligned grain flow, which enhances toughness
Minimal inside voids, decreasing defect risk
Superior fatigue and affect resistance, best for worrying applications
Key Advantages of High-Quality Forged Products
Higher Mechanical Strength
Forging refines microstructure and aligns grains along the geometry, offering 10–30% higher tensile strength compared to similar cast parts.
Unmatched Fatigue Life
Forged components hold up under repeated loading—common in rotating shafts, large gears, and heavy-duty pressure fittings.
Defect-Free Interior
Forged parts show significantly lower porosity and better metallurgical integrity vs. cast parts, which can save millions in field failures.
Precision + Efficiency
Even without complex geometry, forging reduces machining time, reduces material waste, and speeds up delivery cycles.
Common Forged Products We Supply
Shafts & Tubes – Powertrain, marine drive-shafts, turbine spindles
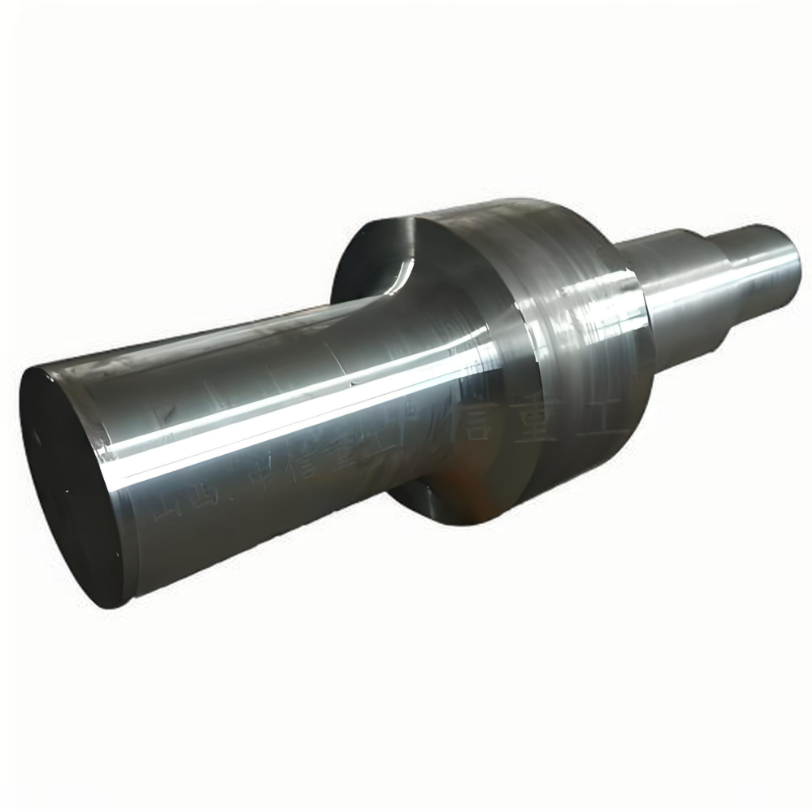
Flanges & Couplings – Pressure-rated components for BOP, pipeline, industrial systems
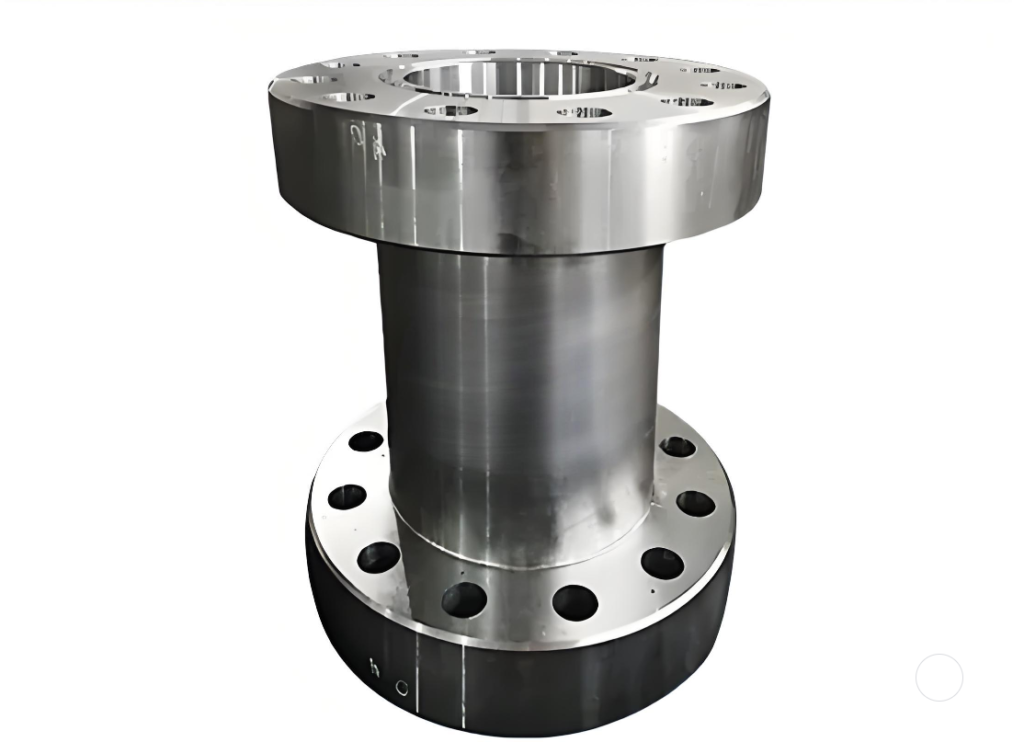
Discs & Rings – Turbine and compressor discs that demand grain continuity
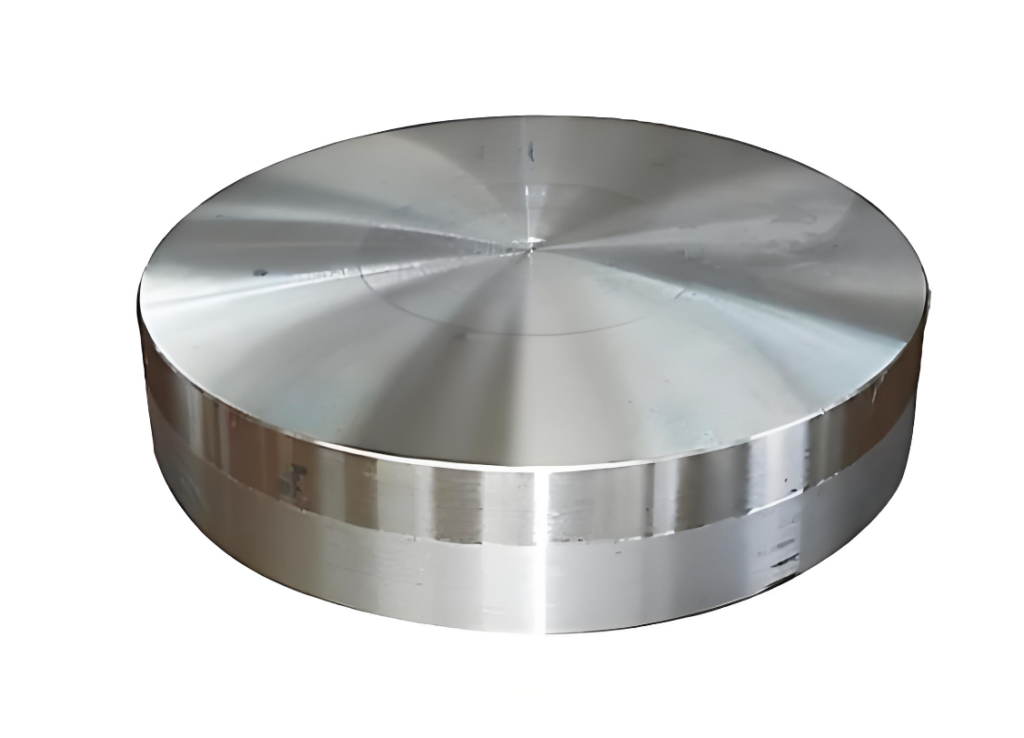
Hooks, Hooks Collars, Tools – Oilfield fishing tools and rig hardware
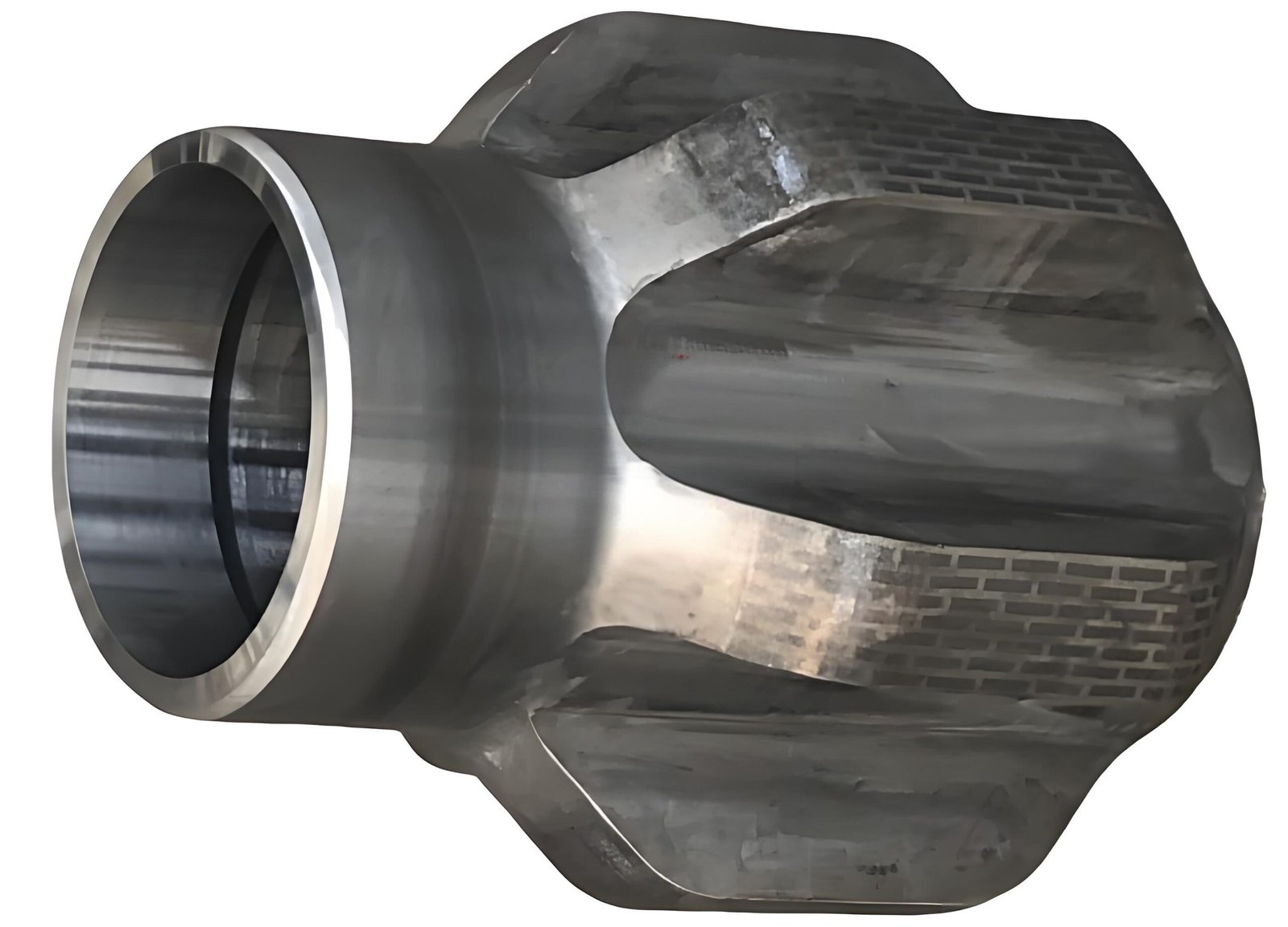
Valves & BOP Parts – Bodies, spools, pistons, formed to API or custom specs
Materials & Standards
We accommodate diverse metallurgy needs:
Carbon & alloy steels (SAE 1045, 4140, 4340, F22, F91)
Stainless steels (304, 316L, 17-4PH)
Nickel alloys (Inconel 625, Hastelloy)
Aluminum alloys (for lightweight, strength-critical uses)
Standards: API 6A/6B/20E, ASTM A105/A182, ISO 9001, NADCAP-capable.
Is Forging Right for Your Application?
Need | Go Forged If… |
Maximum strength | Loads >10 kN/mm², safety-critical |
High fatigue cycle | Thousands or millions of cycles |
Peace of mind | Zero tolerance for defects |
Large quantities | Forge tooling amortizes rapidly |
Medium/simple shapes | Forgings with near-net form |
Why Tiptop Forging Leads the Pack
Advanced Die & Press Capabilities – Medium & large-scale production
Custom Heat Treatment – In-house normalization, quench-temper
Full Quality Traceability – Mill certs, hard tests, ultrasonic & PMI
Global Shipping – Secure export packaging & logistics
Technical Support – Forging design optimization & cost-saving insights
Ready to Curate Superior Forged Products?
Whether it’s a forged shaft, steel disc, valve body, or custom part, we’re here to support. Send us drawings, specs & project details—our engineers will help you determine the ideal forging route.
Final Takeaway
Forged products are the backbone of durable, safe, and high-performance machinery. Choosing forging over casting can be the difference between long-term reliability and costly field failures. At Tiptop Forging, we help you make that choice with confidence—on time, on budget, and with peace of mind.